imported_Dave KG
New member
The standard rotary polishing method is based on what has been named the Zenith Point technique, where you start the machine at slow speed to spread the polish and then build to the working speed and work until the residue goes clear before dropping back down the speeds to refine. This has been a standard working method for some time with proven results.
With some polishes, however, it is possible to extend the work time by using a Regnerating method and this extended work time allows the abrasives to be more fully broken down giving small benefits in terms of correction achieved and bigger benefits in terms of the clarity of the finish - you are essentially extending the burnishing or jeweling stage of your set.
The videos below show typical regenerating sets - first one with Menzerna Intensive Polish and the second one with Chemical Guys V36:
2 Menzerna Intensive Polish Regenerating Set - YouTube
1 Chemical Guys V36 Long Set - YouTube
The idea here is that once the polish residue has gone clear at the working speed, slow down and lighten the pressure and then the residue will come back, hten go back up to a working speed and work until clear and again, then come back down the speeds. You can repeat this process until the polish residue no longer comes back, giving you an extended work time.
This method with Intensive Polish delivered the following results. Panel before:
Panel after (no further refining carried out, this is the finish straight from Intensive Polish):
The technique's extended set lengths allow the abrasives to be more fully broken down which results in slightly better correction where required, but also allows middle of the rod work horse polishes such as Intensive Polish to be brought to a finish which will begin to rival that of finishing polishes - hologram free with good clarity. Intensive Polish can be worked to a hologram free finish with the standard Zenith point method, but this technique in my experience allows or greater clarity from the product through the extended work times
With some polishes, however, it is possible to extend the work time by using a Regnerating method and this extended work time allows the abrasives to be more fully broken down giving small benefits in terms of correction achieved and bigger benefits in terms of the clarity of the finish - you are essentially extending the burnishing or jeweling stage of your set.
The videos below show typical regenerating sets - first one with Menzerna Intensive Polish and the second one with Chemical Guys V36:
2 Menzerna Intensive Polish Regenerating Set - YouTube
1 Chemical Guys V36 Long Set - YouTube
The idea here is that once the polish residue has gone clear at the working speed, slow down and lighten the pressure and then the residue will come back, hten go back up to a working speed and work until clear and again, then come back down the speeds. You can repeat this process until the polish residue no longer comes back, giving you an extended work time.
This method with Intensive Polish delivered the following results. Panel before:
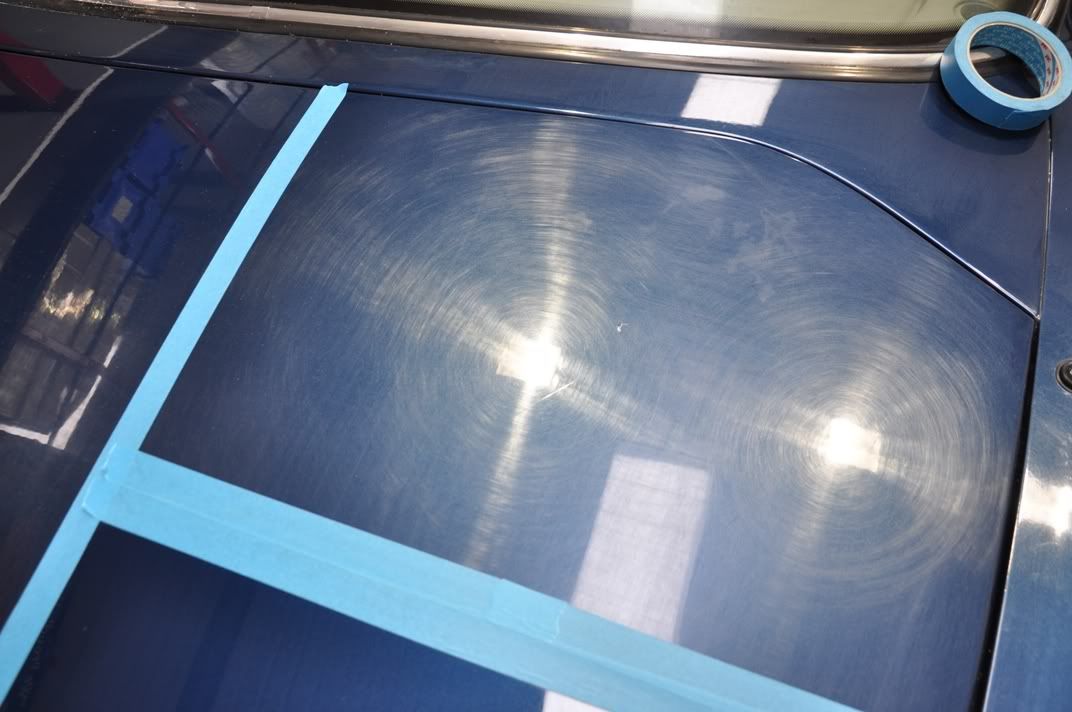
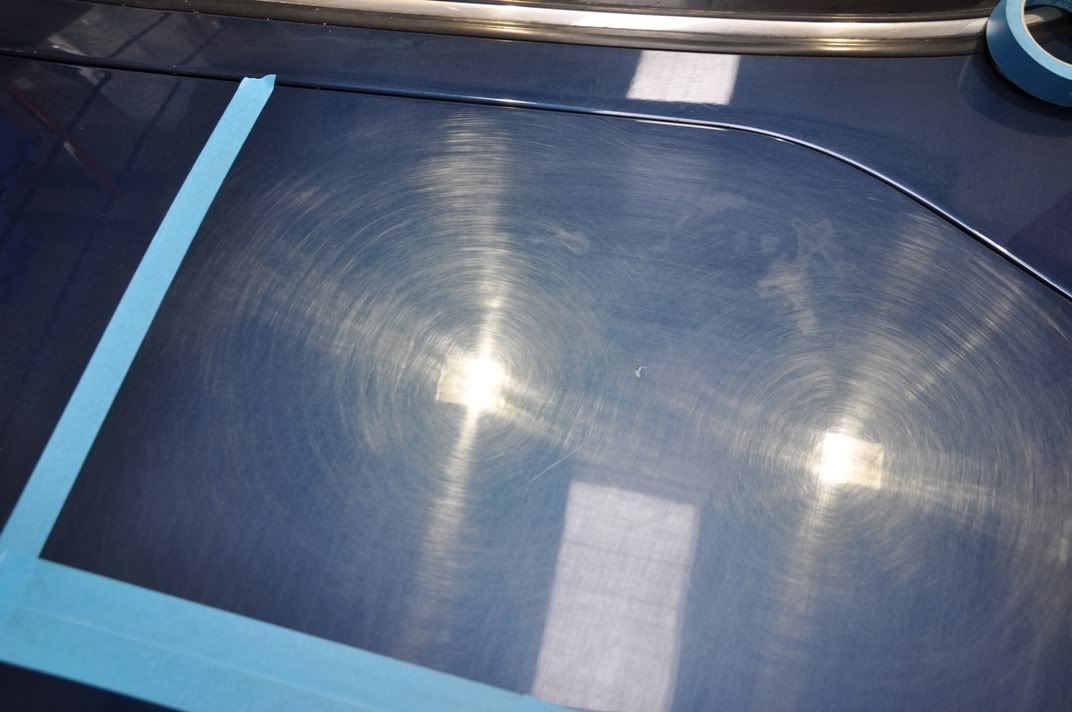

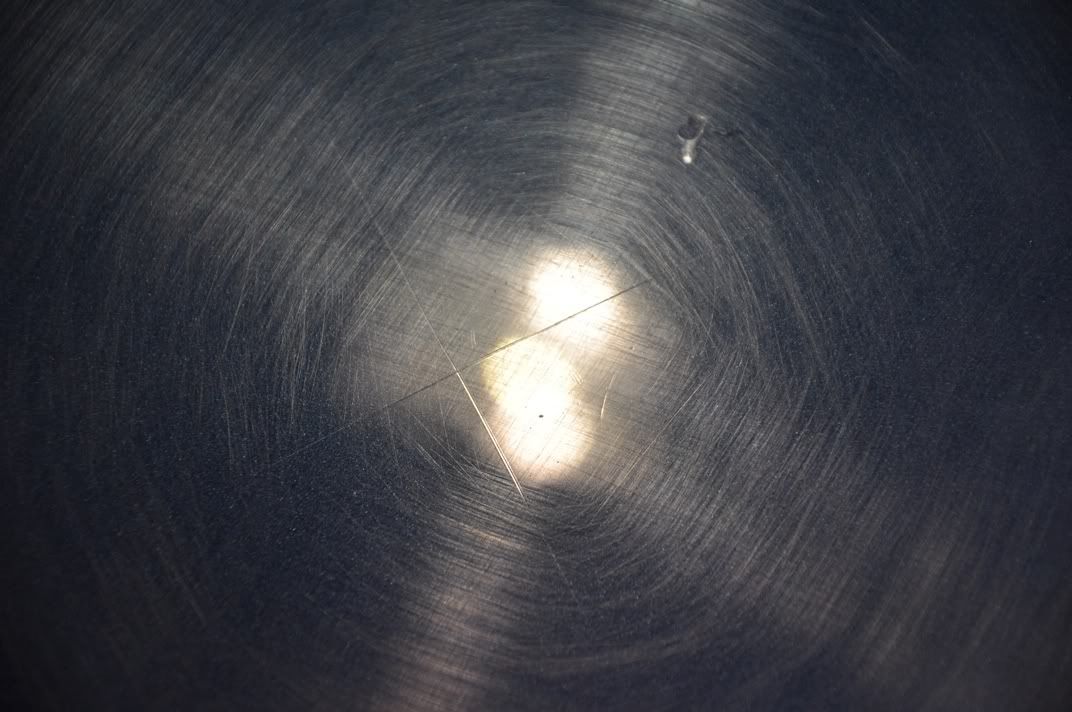
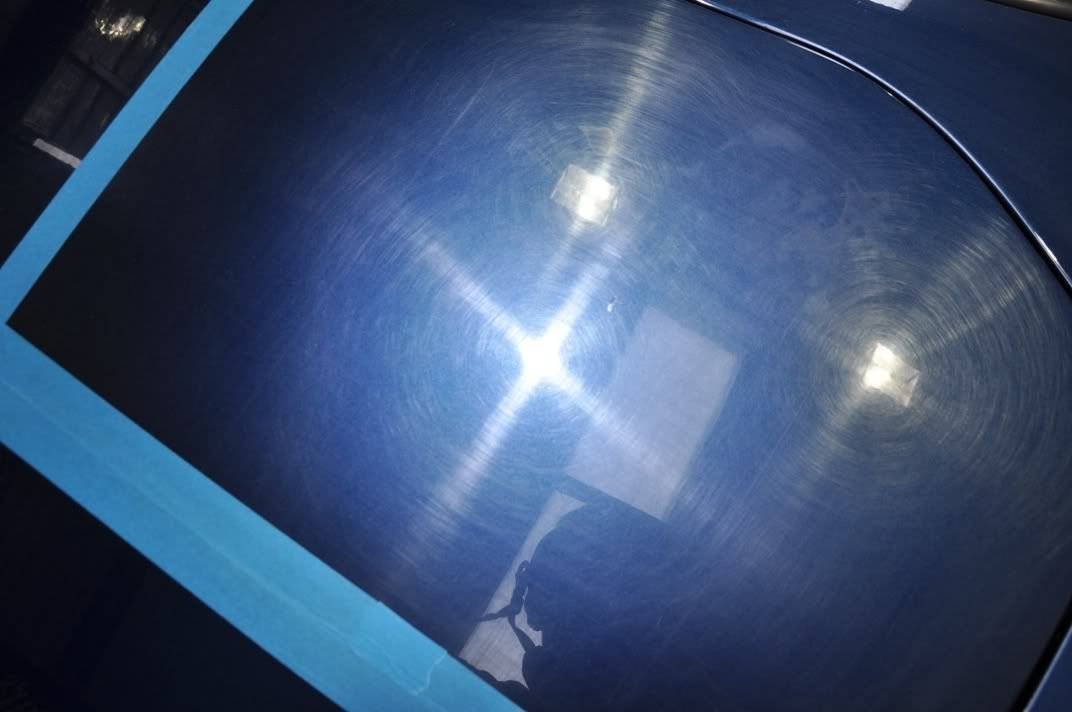

Panel after (no further refining carried out, this is the finish straight from Intensive Polish):
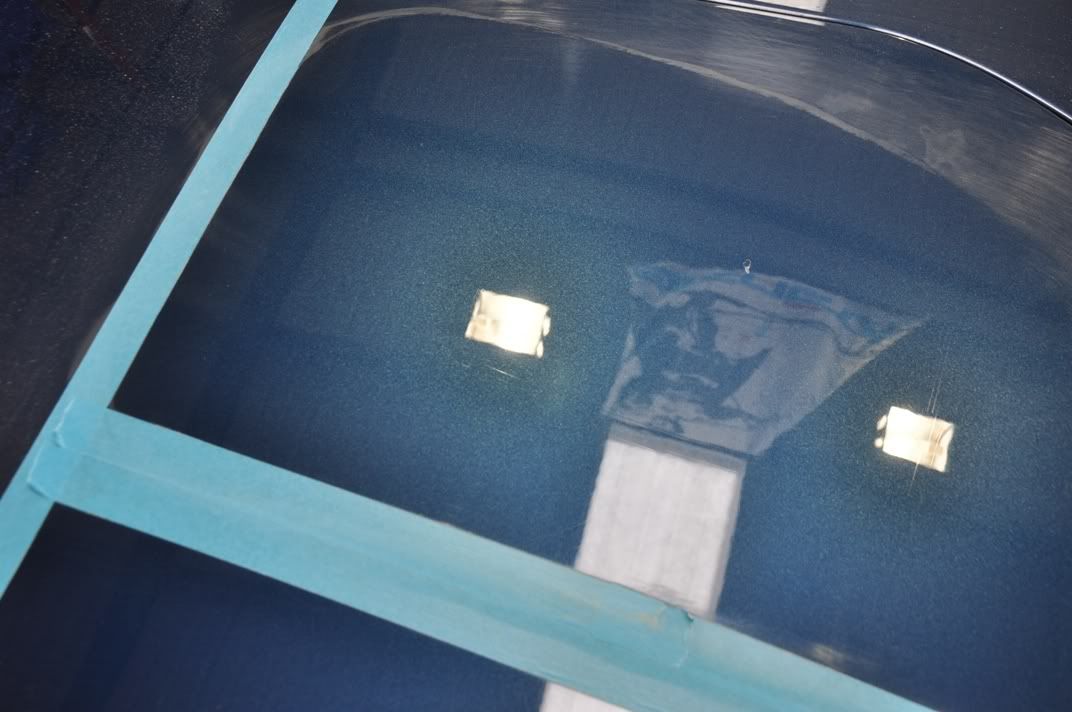
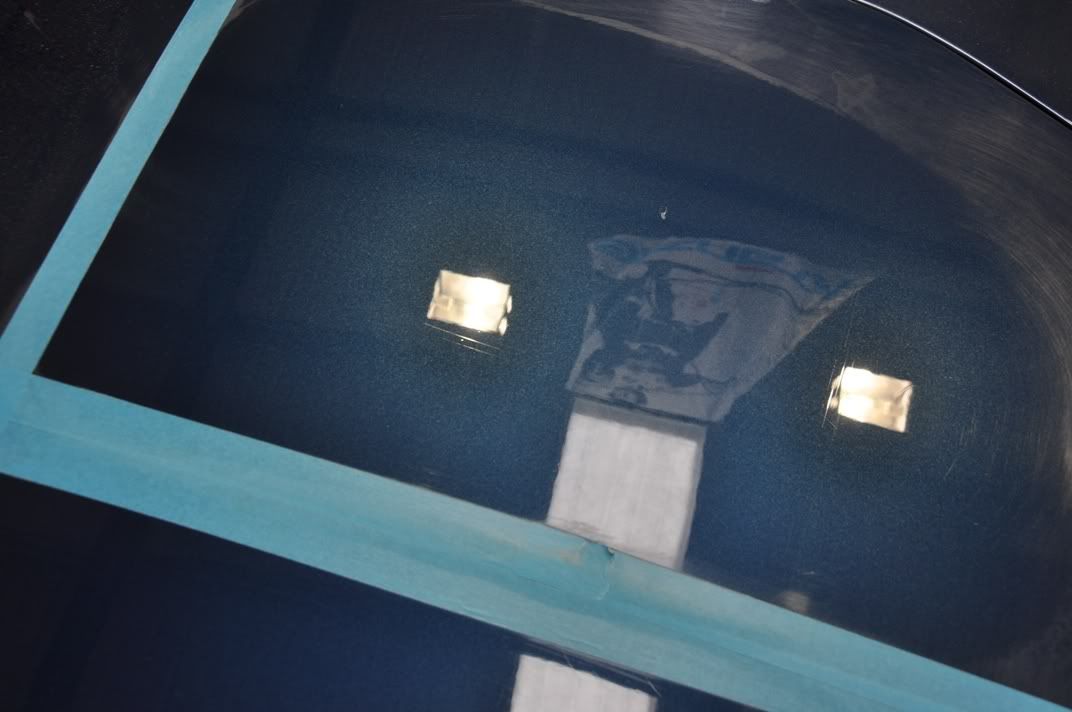

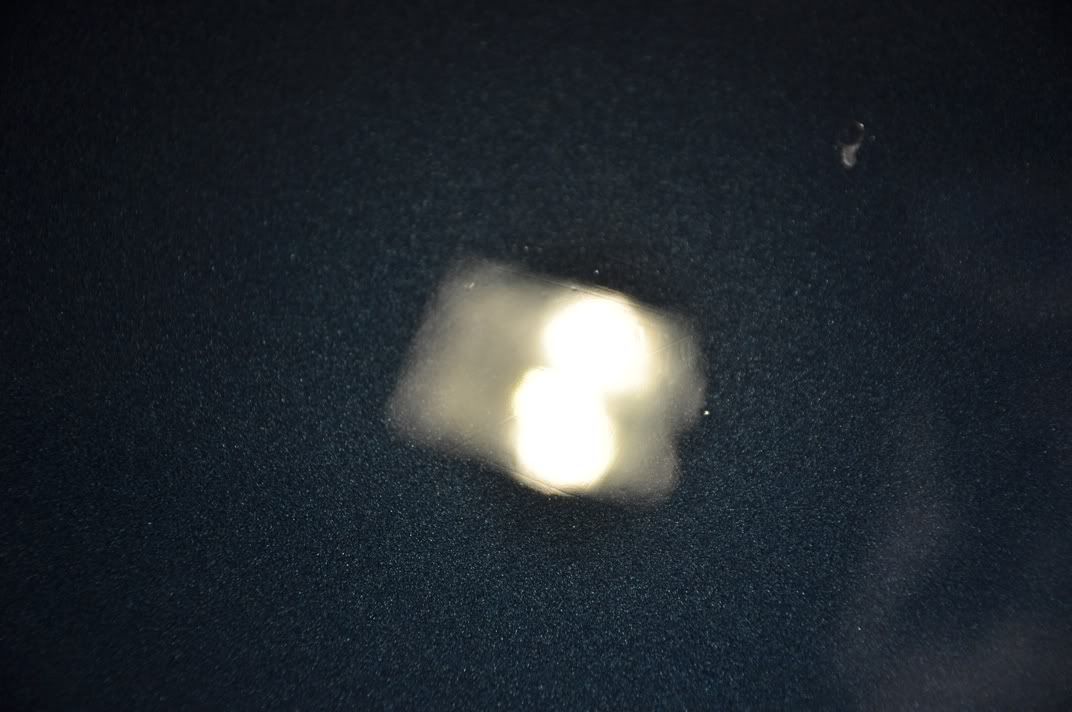
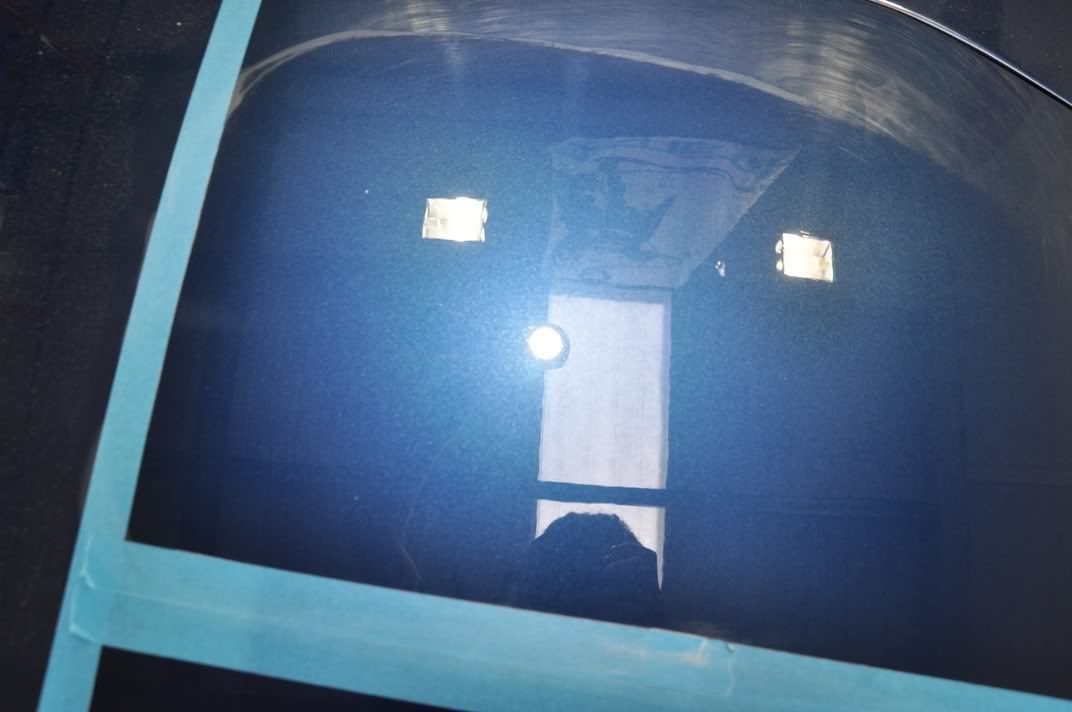
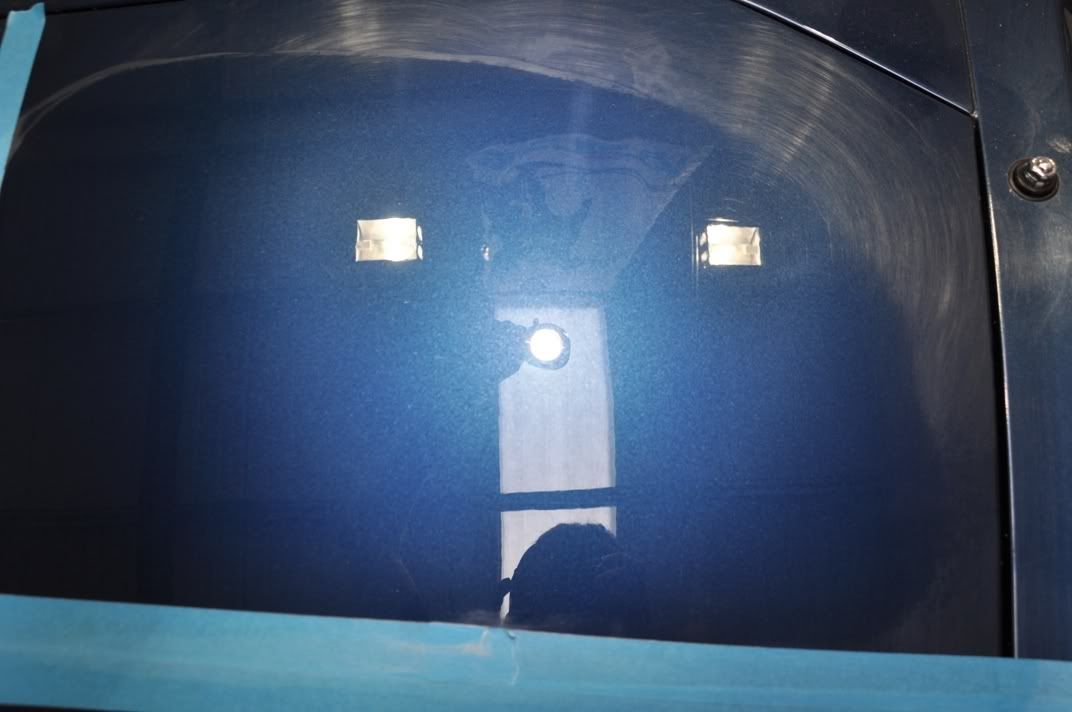
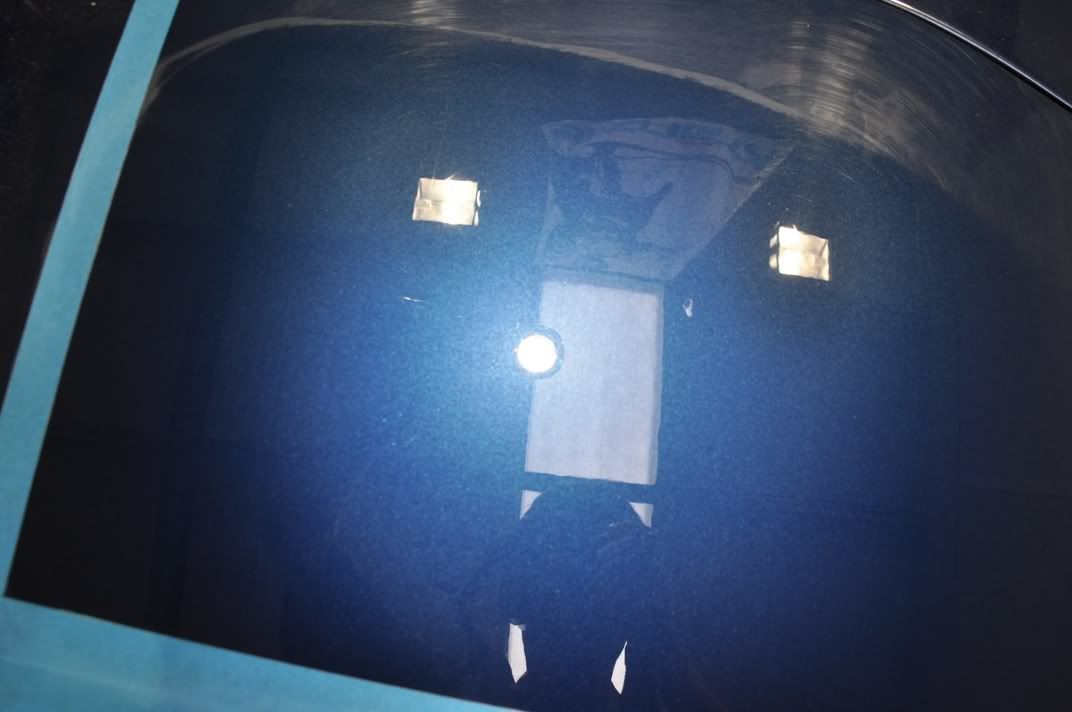
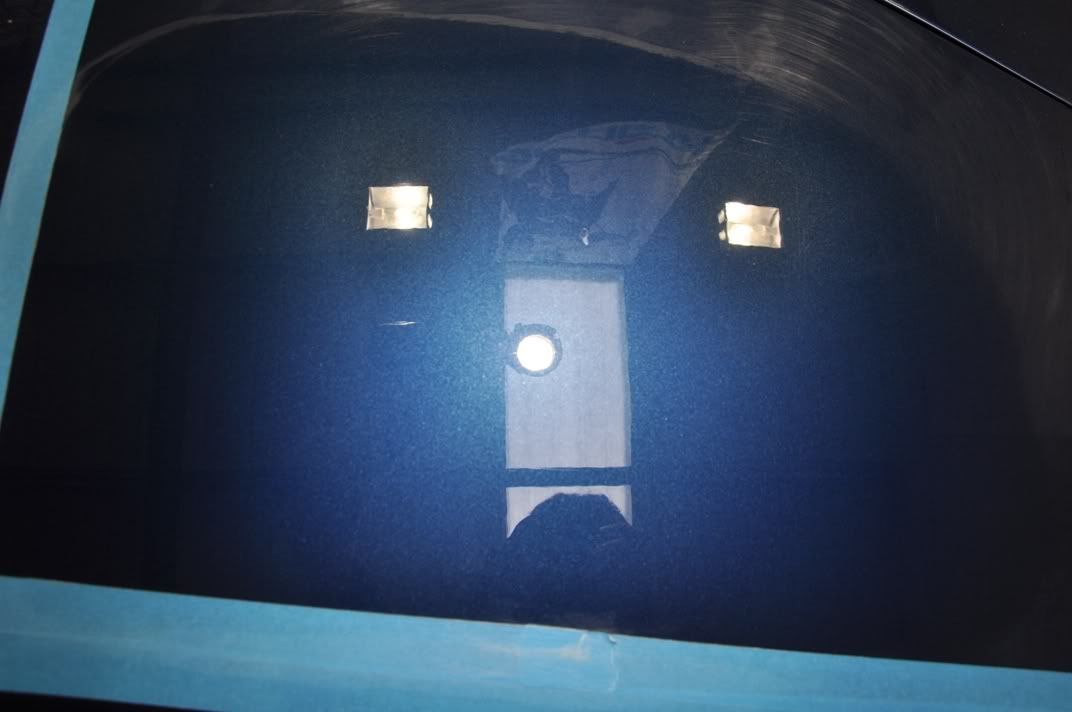
The technique's extended set lengths allow the abrasives to be more fully broken down which results in slightly better correction where required, but also allows middle of the rod work horse polishes such as Intensive Polish to be brought to a finish which will begin to rival that of finishing polishes - hologram free with good clarity. Intensive Polish can be worked to a hologram free finish with the standard Zenith point method, but this technique in my experience allows or greater clarity from the product through the extended work times
